COLEMAN
MICROWAVE COMPANY
P.O. Box 247, 109 Molineu RD
Edinburg, VA 22824
Phone 540-984-8848Fax 540-984-4561
Email coleman@colemanmw.com
INTRODUCTION
It is the policy of Coleman Microwave Company (CMC) to assure
that it's customers products and services fulfill all performance requirements and reflect
the highest quality standards while maintaining timely deliveries.
Coleman Microwave's Quality System is based upon the concept
of every employee's participation in a total quality effort from design to delivery. The
critical impact of design and workmanship on the end product performance and reliability
has been recognized.
Coleman management is dedicated to the successful manufacture
of high quality devices. The policy and procedure set forth in this document will serve to
establish those controls and function to achieve the desired results.
Kenneth R. Coleman Sr. President
Dana A. Braithwaite Manager of Operations

1.0 SCOPE
1.1 The quality assurance system encompasses:
personnel, purchase and receipt of parts and materials, identification, stocking and issue
of parts and materials, the entire process of fabrication and manufacture, packaging,
storage, and shipping.
1.2 The system is designed to assure that the supplies
and/or services, manufactured or performed at CMC or at supplier facilities are subject to
adequate control of quality to ensure customer satisfaction.
1.3 The system is design to provide early detection of
discrepancies and positive corrective action.
1.4 Written inspection and test procedures are
prepared to supplement applicable drawings and other specifications to the extent
necessary.
1.5 The system is designed to provide for quality
control audits to provide an assurance that the quality control system is functioning in
accordance with this manual.
2.0 RESPONSIBILITY/CONTRACT REVIEW
2.1 The quality assurance function reports directly to
the company President.
2.2 The quality assurance function has the following
responsibilities:
2.2.1 Interpretation of conformance to customer
quality requirements.
2.2.2 Review of customer drawings and specifications.
2.2.3 Determination of necessary inspection points.
2.2.4 Documentation of the necessary inspection
instructions including change control.
2.2.5 Planning, developing, initiating, coordinating,
implementing, and maintaining the most efficient and effective procedures for optimum
quality assurance.
2.2.6 Maintenance of adequate quality assurance
records.
2.2.7 Review of quality assurance records to provide
for internal corrective action follow-up.
2.2.8 Vendor quality assurance and corrective action
follow-up.
2.2.9 Initial and continuing periodic inspection of
all standard and special gages, test equipment, and tooling used for manufacturing.
2.2.10 Coordination of internal corrective action on
items rejected by the customer, including notification of corrective action taken and
evaluation of effectiveness of the action.
2.2.11 Quality control audits, done in accordance with
Coleman's Quality Procedure #16.
2.2.12 Assure that the inspection function is capable
of rendering an unbiased decision to accept or reject any material inspected.
2.2.13 Each contract and/or customer purchase order,
upon receipt is reviewed for pertinent quality requirements. This review includes
completion of a Sales Release and Planning Document.
2.2.14 All quality requirements are documented on the
Sales Release Planing Document form.
2.2.15 A notebook of the SRPD forms for all active
projects is maintained.
2.2.16 A working file is established for each project
and contains the applicable drawings, inspection records, inspection and test plans, etc.
3.0 GENERAL POLICIES
3.1 Coleman Microwave Company will notify customers in
writing of system changes, and will comply with the customers concerning the changes.
3.2 Coleman Microwave Company does not use inspection
equipment that is not specified in Customer/Government contracts
3.3 Coleman Microwave Company permits
Customer/Government to evaluate inspection system and supplies, and allows the
Customer/Government to make verification and evaluations to determine inspection system
effectiveness.
Coleman Microwave Company
Controlled Quality Manual Serial Number Check List
REV LEVEL - DATE
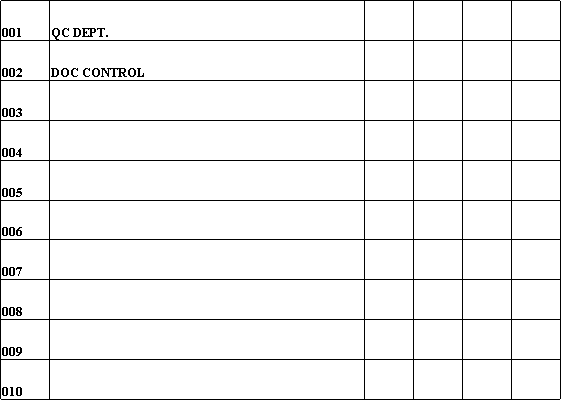
QUALITY ASSURANCE FORMS
TABLE OF CONTENTS
PAGE NO/REV LEVEL
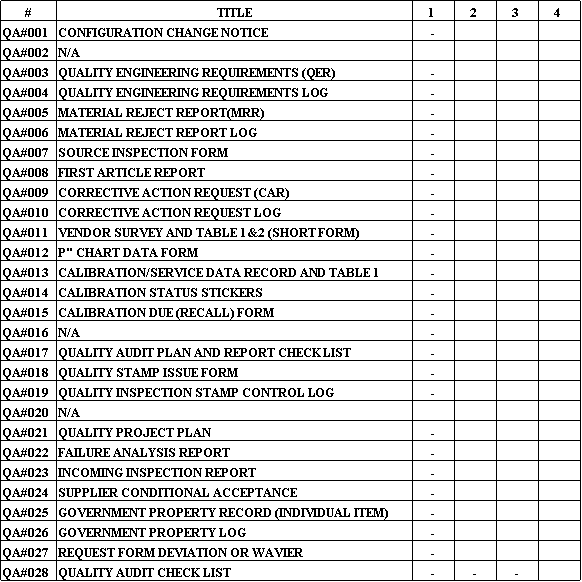
QUALITY PROCEDURES
TABLE OF CONTENTS
PAGE NUMBER/REV LEVEL
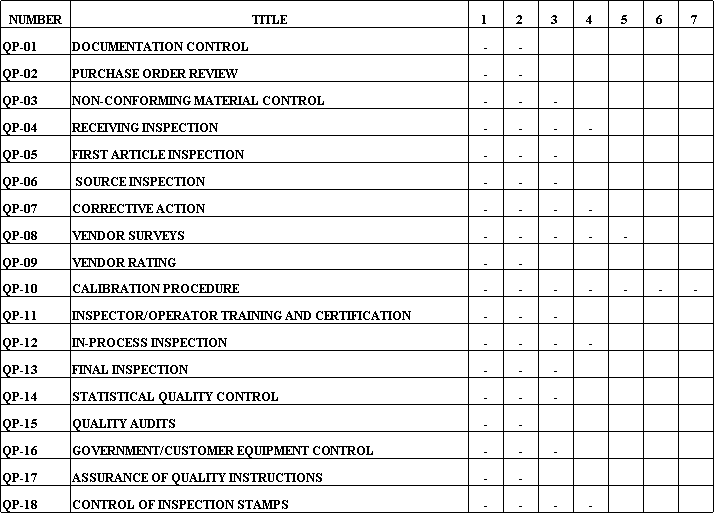
QP #01
POLICIES AND PROCEDURES
QUALITY PROCEDURE
SUBJECT: DOCUMENTATION CONTROL & REVIEW
1.0 PURPOSE
This procedure describes the system for quality assurance to
review and critique engineering and supplemental documentation for adequacy, completeness,
and to monitor in-house and subcontractor operations to see that approved changes are
incorporated at the designated point.
2.0 APPLICATION
The procedure applies to all released materials including
engineering drawings, specifications, process instructions, production engineering
instruction, industrial engineering instructions, design-related work instructions, and
engineering changes. CHANGES TO CUSTOMER DRAWINGS ARE EXPRESSLY PROHIBITED.
3.0 PROCEDURE
3.1 Quality engineering of quality assurance has the
prime responsibility for documentation review and the drafting department has
responsibility for control. In performing this work, quality engineering will participate
in design reviews and will be the quality assurance representative on the change.
3.2 Engineering drawings are to be reviewed for
adequacy, completeness, and with corrective action taken regarding discrepancies.
3.3 Engineering is to verify that documents received
for application are properly released and authorized.
3.4 Audits are to be conducted periodically and on a
random basis to see that only current material is being distributed and used, and that
obsolete material has been removed.
3.5 Drafting department is responsible for insuring
all drawings, part lists, ECN's, etc... are dated and signed.
3.6 As a participant on the Change Control Board,
Engineering is to review Engineering Change Notices (ECNs) to determine if they are
correct, complete, and in compliance with standards and needs.
3.7 Quality engineering will maintain a drawing
revision log, listing all appropriate information as follows: drawing number, ECN number,
description, rev level, change date.
3.8 The drafting department will provide quality
assurance with a hard copy print out of all drawings in house, if applicable.
3.9 When sending prints and/or films out for
reproduction or to subcontractors, the drafting technician will provide purchasing with
all requested prints and/or films listed on the approved purchase request order.
3.10 Drafting department will maintain a log of
customer prints, listing all appropriate information as follows: drawing number, ECN
number, layer number, description, part number, and comments, etc.
4.0 ASSOCIATED DOCUMENTS
CMP #0055
CMP #0032
CMP #0034FORMS
QA #001
QP #02
POLICIES AND PROCEDURES
QUALITY PROCEDURE
SUBJECT: PURCHASE ORDER REVIEW
1.0 PURPOSE
This procedure sets forth a method for reviewing purchase
orders, prior to their issuance, to assure that contractual and quality requirements have
been properly incorporated.
2.0 APPLICATION
This procedure applies to the procurement of all materials,
parts, and assemblies that will be used in actions of both the purchasing department and
quality engineering.
3.0 PROCEDURE
3.1 Prior to issuance, the purchasing department is to
forward purchase orders to the quality engineering department for review.
3.1.1 Notification that this quality procedure is
imposed will be accomplished by test on Coleman Microwave Company sales order form stating
"CMC QP #02 is imposed".
3.2 Quality engineering is to review these procurement
documents to determine if all contractual and quality requirements have been adequately
specified.
3.3 Each purchase order is to be augmented with the
appropriate instructions.
3.4 Each purchase order is to specify that company
procurement personnel, quality assurance personnel, and engineering personnel will have
access to the supplier's or subcontractor's premises.
3.5 ALL QUALITY REQUIREMENTS SHALL BE SPECIFICALLY:
A) Called out on Q.E.R. (QA #003) and be forwarded to
purchasing agent for incorporation on/or attached to purchase order prior to purchasing
fabricated or modified material.
B) All Q.E.R.'s are to be numbered and entered into the
Q.E.R. computer log
(QA #004).
3.6 If there are discrepancies in the purchase order,
it is to be returned to the purchasing department accompanied by a description of the
problem.
3.7 If the purchase order is determined to be adequate
from a quality requirement standpoint, it is to be signed as approved by the quality
engineer and returned to the purchasing department.
3.8 The quality assurance department is to maintain
records of the review and disposition of procurement documents (QA #004).
3.9 When Government inspection is required Coleman
Microwave Co. agrees to add to the purchasing document the following statement:
"Government inspection is required prior to shipment from your plant. Upon receipt of
this order, promptly notify the Government Representative who normally services your plant
so that appropriate planning for Government inspection can be accomplished."
QP #03
POLICIES AND PROCEDURES
QUALITY PROCEDURES
SUBJECT: NON-CONFORMING MATERIAL CONTROL
1.0 PURPOSE
This procedure defines a system that identifies and controls
material that does not conform to specification.
2.0 APPLICATION
This procedure applies to all defective material produced by
or for this company.
3.0 ASSOCIATED DOCUMENTS
3.1 QUALITY PROCEDURE
All remaining quality procedures.
3.2 FORMS
QA #005, QA #006, QA #012
4.0 PROCEDURE
4.1 Any material rejected by quality control via
received inspection, in-process inspection, final inspection, audits, or any other quality
activity that may designate non-conforming material reject report (Form No. QA-005). A red
tag will be attached to all non-conforming material identifying MRR No., Part No., Serial
No., Quantity, Inspection stamp and Date.
4.2 Any material found by other departments that is
discrepant will be delivered to quality control. This material must be accompanied by the
following information:
1.PART NUMBER; P.O. # AND S.O. #
2.QUANTITY
3.DISCREPANCY
Quality control will generate all material reject reports.
4.3 All non-conforming material will be secured in a
locked hold area, when practical, with the MRR and red tag attached.
4.4 All non-conforming material must have a
preliminary review by quality engineering and/or manufacturing engineering within two
working days. Quality assurance will keep all non-conforming material information in a log
book
(QA #006).
4.5 The preliminary review can make the following
dispositions without the customers concurrence.
1.NO DEFECT
2.REWORK
3.100% SORTING OF PRODUCT
4.SCRAP
5.RETURN TO VENDOR
6.MRB (REPAIR)
4.6 Materials that cannot be dispositioned by the
preliminary review must be held for a material review board (MRB).
4.6.1 Material review board is required when customer
approval is required to repair units. NOTE: 1. Definition of "repair" is to
form, fit function can not meet print conformance. 2. Definition of "rework" is
return to print conformance.
4.7 For material reject reports that have been
disposition for corrective action, quality assurance will issue corrective action requests
per requirements of procedure no QP 07 (QUALITY PROCEDURE FOR CORRECTIVE ACTIONS).
4.8 Quality assurance will keep all MRR's on file
under program or customer name. These reports are the only means for handling
non-conforming material. All the history of preliminary review, MRB activities, and final
disposition of the product is to be documented on the MRR.
4.9 Material returned from customer must be forwarded
to quality control for processing on incoming inspection report form (QA #023).
4.10 All customer returned material shall be inspected
per QA-05 (RECEIVING INSPECTION).
4.11 After inspection, the Quality Control function
shall determine responsibility for the returned material.
4.12 The Quality Control Department shall insure that
prompt corrective action QA #009 is taken to correct assignable conditions which have
resulted or which could result in the submission to a customer of supplies which do not
conform to: (1) The quality assurance provisions of the item and customer, (2) Inspections
and test required by contract, and (3) Other inspections and test required to substantiate
product conformance.
4.13 The Quality Control Function shall retain a file
of all returned customer material and of all action taken.
QP #04
SUBJECT: RECEIVING INSPECTION
1.0 PURPOSE
This procedure describes the system for inspecting material
received from suppliers and subcontractors or customer returns.
2.0 APPLICATION
This procedure applies to the inspection of all material
received.
3.0 ASSOCIATED DOCUMENTS
3.1 QUALITY PROCEDURES
QP-02PURCHASE ORDER REVIEW
QP-04NONCONFORMING MATERIAL
QP-05FIRST ARTICLE INSPECTION
QP-07SOURCE INSPECTION
QP-08CORRECTIVE ACTION
QP-16GOVERNMENT/CUSTOMER PROPERTY
3.2 FORMS
QA #005, QA #006, QA #007, QA #012, QA #023
4.0 PROCEDURE
4.1 All materials which are to be inspected upon
receipt are to be inspected by receiving inspection in terms of compliance to specified
requirements, completeness, transit damage, and proper and complete paper work
documentation.
4.2 Parts that have been sent out for special
processing are to be inspected, when returned, only for the processing performed.
4.3 Measuring and test equipment devices that have
been sent out for calibration and/or repair, when returned, are to be forwarded to the
quality control department for processing.
4.4 Materials that have been source inspected, upon
receipt, are to examined only for transit damage, and the completeness and correctness of
the accompanying paper work and documentation (such as certificates and test reports).
Refer to QP 06. A copy of Form No. QA-007) will be included with the shipment.
4.5 All incoming materials are to be processed in the
priority sequence of the dates when the materials are required.
4.6 As a prelude to inspecting received materials,
obtain specifications, purchase orders, and prints.
4.7 All material lots may be subjected to sampling
inspection. The acceptance quality level (AQL) is determined by supplier statistical trend
data.
4.8 The materials are to be inspected for conformance
to requirements and the results are to be recorded on the P chart data form.
4.9 If the purchase order designates that a first
article inspection is required, refer to QP-05.
4.10 Material that has been accepted as a result of
receiving inspection will be tagged with a green tag identifying purchase order number,
part number, serial number, (if applicable), quantity, and date. Stamp tag with acceptance
and dated on the material moved to the stockroom.
4.11 Materials that have been rejected will be tagged
with a red tag identifying MRR number, part number, purchase order number, serial number,
(if applicable), quantity, inspection rejection stamp and date. A MRR (form No. QA-005)
will be generated and the non-conforming material will be processed per QP-04, this
material is held in a bonded storage area until disposition can be made.
4.12 If the disposition on the material reject report
calls for corrective action for the supplier, refer to QP-08 (Quality Procedure For
Corrective Action).
4.13 All inspection records, test data, certificates
of compliance, and material certification will be kept on file at receiving inspection.
4.14 Customer/Government material received will be
handled in accordance with
QP-16, Government property.
5.0 RAW MATERIAL CONTROL
5.1 Raw material are those received in an unfinished
form (i.e. metal, plastic, rubber, castings, paint, chemicals, etc.).
5.2 All raw materials are inspected by the receiving
inspection function.
5.3 Accepted materials are identified by inspection
utilizing a stamp, tag or color code, then released to the stockroom.
5.4 Non-conforming material is processed in accordance
with QP-03 of this manual.
5.5 Corrective action is taken in accordance with
QP-07 of this manual.
5.6 Copies of all certifications when required, are
filed with the applicable Purchase Order and are available for review upon customer
request.
5.7 Verification of suppliers certifications may be
accomplished by independent testing laboratories to comply with customer purchase order
requirements. Verification is done is accordance with QP-09 of this manual.
5.8 Limited Life Materials are additionally identified
with "DO NOT USE AFTER (MM/DD/YY)", information. Materials not totally
used prior to the end of their limited use are removed from service.
5.8.1 It shall be the Area Supervisor's responsibility
to insure that all materials in their department are current and not out dated. It is also
their responsibility to dispose of any out dated materials in their department.
5.9 Certified stock is issued from the raw material
storage area to comply with the requirements of the applicable drawing or specification.
5.10 When required by contract, raw material shall be
marked so that it is certifiable and traceable to one sales order, purchase order, heat
number, etc.
6.0 TRACEABILITY
6.1 The purpose of this procedure is to establish
traceability of raw materials when traceability is required by contract specification.
6.2 Any contract requiring traceability will be so
noted on the sales release form.
6.3 Purchasing will take note of any sales release
that specifies traceability and will submit the purchase orders for this contract to
Quality Engineering for compliance to QP-02.
6.3.1 Upon receiving the raw materials in inspection,
the inspector will check the sales order to determine if traceability is needed. If
traceability is needed the inspector will identify such raw material with the approved tag
or lot slip and inspection stamp.
6.3.2 A traceable raw material tag or slip will stay
with the raw material unit until either the material is used and a new inspection slip or
tag is issued for the resultant part.
QP #05
POLICIES AND PROCEDURES
QUALITY PROCEDURE
SUBJECT: FIRST ARTICLE INSPECTION
1.0 PURPOSE
This procedure defines a method for inspecting the first of a
series of articles produced for the purpose of early detection and timely correction of
discrepancies.
2.0 APPLICATION
This procedure applies to the first of all new or
significantly changed parts and assemblies manufactured for the company by subcontractors,
or the first part or assembly manufactured for the company by a new subcontractor or by
CMC manufacturing.
3.0 ASSOCIATED DOCUMENTS
FIRST OPERATION, FIRST PIECE
FIRST ARTICLE REPORT PROCURED MATERIAL
3.1 FORMS
CMP #0043, QA #008
4.0 PROCEDURE - SUPPLIER
4.1 The quality engineering department is responsible
for citing on a purchase order or contract the requirement for a first article inspection
4.2 First article inspection could be performed in the
receiving inspection area or the inspection can be performed by source inspection
personnel at the subcontractor's facility if so authorized by the quality assurance and
purchasing department per QP-02.
4.3 The first article inspection is to be a complete
one, covering all appropriate physical and functional characteristics of the part or
assembly, workmanship, and the completeness and correctness of the required documentation.
First article material will be tagged with a white tag identifying purchase order no.,
part no., serial no., inspection acceptance stamp and date. The white tag will remain with
first article material.
4.4 The test engineering department is responsible for
providing the required test equipment, test equipment operating specifications and test
personnel to perform tests required.
4.5 The quality engineering department is responsible
for providing the receiving inspection department with the required inspection
instructions per QP-17.
4.6 If special analysis or tests are required,
receiving inspection is to forward the part or assembly to the appropriate department or
function.
4.7 At the completion of their first article
inspection, the inspector is to prepare the first article report - procured material. The
form is to be filled out as follows:
1. NAME AND ADDRESS OF THE SUBCONTRACTOR
2. DATE OF THE REPORT
3. REPORT NUMBER
4. PART OR ASSEMBLY NUMBER
5. REVISION NUMBER
6. PART OR ASSEMBLY NAME
7. NEXT ASSEMBLY
8. PURCHASE ORDER OR CONTRACT NUMBER
9. CHECK MARK FOR APPROVAL
10. CHECK MARK FOR REJECTION
11. IF REJECTION, DESCRIPTION OF THE DISCREPANCY
12. RECOMMENDED DISPOSITION
13. A CHECK MARK TO INDICATE WHETHER OR NOT A TEST REPORT IS
ATTACHED
14. DATED SIGNATURE OF THE INSPECTOR
15. DATED SIGNATURE OF THE PERSON AUTHORIZED TO APPROVE THE
REPORT
4.8 COPIES OF THE REPORT ARE TO BE DISTRIBUTED AS
FOLLOWS:
1. RECEIVING INSPECTION FILES
2. PURCHASING (FOR FORWARDING TO THE SUBCONTRACTOR).
5.0 PROCEDURE - CMC MANUFACTURING
5.1 CMC manager will be responsible for requesting
first article inspection and implementing appropriate step on manufacturing routing, tag,
traveler, etc.
5.2 First article inspection is to be a complete one,
covering all appropriate physical and functional characteristics of the part of assembly,
workmanship, and the completeness and correctness of the required documentation. First
article material will be tagged with a white tag identifying purchase order no., part no.,
serial no., inspection acceptance stamp and date. The white tag will remain with first
article material.
5.3 If special analysis or tests are required, quality
control inspection is to forward the part or assembly to the appropriate department or
function.
5.4 At the completion of the first article inspection,
the inspector is to prepare Form #, QA #008. The form is to be filled out a follows:
1. NAME AND ADDRESS OF THE SUBCONTRACTOR
2. DATE OF THE REPORT
3. REPORT NUMBER
4. PART OR ASSEMBLY NUMBER
5. REVISION NUMBER
6. PART OR ASSEMBLY NAME
7. NEXT ASSEMBLY NUMBER
8. PURCHASE ORDER OR CONTRACT NUMBER
9. CHECK MARK FOR APPROVAL
10. CHECK MARK FOR REJECTION
11. IF REJECTION, DESCRIPTION OF THE DISCREPANCY
12. RECOMMENDED DISPOSITION
13. A CHECK MARK TO INDICATE WHETHER OR NOT A TEST REPORT IS
ATTACHED
14. DATED SIGNATURE OF THE INSPECTOR
15. DATED SIGNATURE OF THE PERSON AUTHORIZED TO APPROVE THE
REPORT
QP #06
POLICIES AND PROCEDURES
QUALITY PROCEDURES
SUBJECT: SOURCE INSPECTION
1.0 PURPOSE
This procedure describes the approach for the source
inspection of parts or assemblies produced by suppliers and subcontractors.
2.0 APPLICATION
This procedure applies to all supplies and subcontractors and
its application is the responsibility of the Quality Engineering per QP-02.
3.0 ASSOCIATED DOCUMENTS
QP #02, PURCHASE ORDER REVIEW
QP #03, NON-CONFORMING MATERIAL
QP #04, RECEIVING INSPECTION
QP #07, CORRECTIVE ACTION
3.1 FORMS
QA #007
4.0 PROCEDURE
4.1 Source inspection of parts or materials at
supplier's or subcontractor's facility will be performed whenever it is specified as a
requirement on a contract or purchase order. Quality engineering has the option to waive
source inspection and impose receiving inspection.
4.2 The source inspection is made at the point of
fabrication prior to shipment to this company using inspection instructions, drawings, and
specifications, and includes an examination of the supplier's or subcontractor's records
of inspections and tests. The result are recorded on the source inspection report as
follows:
- NAME AND ADDRESS OF THE VENDOR
- PURCHASE ORDER NUMBER
- DATE OF THIS REPORT
- NAME OF THE PROJECT
- LOT OF SERIAL NUMBERS
- A LIST OF THE PART NUMBERS INSPECTED
- QUANTITIES ORDERED FOR EACH PART
- QUANTITIES INSPECTED
- SIZE OF THE SAMPLE, IF APPLICABLE
- QUANTITY ACCEPTED
- QUANTITY REJECTED
- ANY REMARKS
- DESCRIPTION OF THE DRAWINGS AND/OR SPECIFICATIONS INCLUDING
THE REVISION NUMBER
- REASONS FOR REJECTIONS
- A BRIEF DESCRIPTION OF ANY CORRECTIVE ACTION TAKEN BY THE
SUPPLIER
- SUPPLIER'S DATED SIGNATURE
- INSPECTOR'S DATED SIGNATURE
4.3 All material lots may be subjected to sampling
inspection. The acceptable quality level (AQL) is determined by supplier statistical trend
data.
4.4 Material that has been accepted as a result of
source inspection will be tagged with a green tag identifying purchase order no., part
no., serial no., (if applicable). Quantity, inspection acceptance stamp and date.
4.5 Materials that have been rejected will be tagged
with a red tag, identifying MRR generated and the non-conforming material will be
processed per QP-03.
4.6 If the disposition on the material reject reports
call for corrective action of the supplier, refer to QP-07.
4.7 Materials that have been source inspected, upon
receipt at CMC are to examined only for transit damage, and the completeness and
correctness of the accompanying paper work and documentation (such as certificates and
test reports). A copy of the source inspection report will be included with the shipment.
QP #07
POLICIES AND PROCEDURES
QUALITY PROCEDURES
SUBJECT: CORRECTIVE ACTION
1.0 PURPOSE
This procedure specifies a system informing appropriate
personnel and suppliers of instances of non-conformance to quality requirements, and
initiating corrective action.
2.0 APPLICATION
This system encompasses the activities of all departments in
the company and action related to its suppliers. Its operation is the responsibility of
quality engineering.
3.0 ASSOCIATED DOCUMENTS
All CMC quality procedures and process procedures.
3.1 FORMS
QA #009, QA #010, QA #022
4.0 PROCEDURES
4.1 In the event of a material discrepancy requiring
corrective action, Form # QA #009 is issued to initiate an investigation of the cause of
the discrepancy, in order to prevent a recurrence.
4.2 A car can be issued as result of: material review
board, inspection/audits, test/failure reports, customer complaints, and field returns.
4.3 The corrective action request form is to be filled
out as follows:
- The number of the (CAR)
- The name of the person and organization requesting action
- The date of the request
- The date when a reply to the request is due
- The name of the program of project
- The part name
- The part number
- The inspection or failure report number
- The material review report number, if applicable
- A description of the condition
- The apparent cause of the condition, if known
4.4 Information relative to the car is now recorded on
Form # QA # 010 as follows:
- THE CAR NUMBER
- THE INSPECTION OR FAILURE REPORT NUMBER
- THE MATERIAL REVIEW REPORT NUMBER, IF APPLICABLE
- THE NAME OF THE ORGANIZATION RESPONSIBLE FOR THE INVESTIGATION
AND CORRECTIVE ACTION
- THE DATE THE ASSIGNMENT WAS MADE TO THAT ORGANIZATION
- THE DATE when THE ORGANIZATION RESPONSE IS DUE
4.5 The CAR is forwarded to the assigned organization
where an investigation is done to detect the cause of the discrepancy, and action taken to
prevent recurrence. This information is recorded on the CAR form as follows:
- ACTUAL CAUSE OF THE DISCREPANCY
- ACTION TAKEN TO PREVENT RECURRENCE
- THE SIGNATURE AND TITLE OF THE PERSON RESPONSIBLE FOR THE
CORRECTIVE ACTION AND THE DATE OF THE SIGNATURE
4.6 The completed CAR is returned to quality
engineering. The corrective action log is updated.
5.0 PROCEDURE SUPPLIER
5.1 When supplier corrective action is required, a
corrective action request is to be filled out either by the quality engineering or the
quality control department.
5.2 The CAR form is to be filled out as follows:
- THE CAR NUMBER
- THE DATE THE FORM IS BEING PREPARED
- THE NAME AND ADDRESS OF THE SUPPLIER
- THE NAME AND ADDRESS OF THE SENDER
- THE PART NUMBER
- THE QUANTITY OF PARTS REJECTED
- THE QUANTITY REJECTED
- THE NAME OF THE PROGRAM OR PROJECT
- THE PURCHASE ORDER NUMBER AND SALES ORDER NUMBER
- A DESCRIPTION OF THE DISCREPANCY
- A CHECK MARK AS TO THE DISPOSITION TAKEN
- THE APPROVAL SIGNATURE OF THE APPROPRIATE PURCHASING
REPRESENTATIVE
- THE APPROVAL SIGNATURE OF THE APPROPRIATE QUALITY ASSURANCE
REPRESENTATIVE
5.3 The car is to be processed through the quality
engineering unit for logging and control process.
5.4 After logging, the CAR is sent to purchasing for
forwarding to the supplier.
5.5 The supplier investigates the discrepancy and
taken corrective action, to be recorded on the CAR form as follows:
- DESCRIPTION OF THE CAUSE OF THE DISCREPANCY
- A DESCRIPTION OF THE CORRECTIVE ACTION TAKEN TO ELIMINATE A
RECURRENCE OF THE DISCREPANCY
- THE SUPPLIER'S SIGNATURE, TITLE, AND DATE
5.6 The completed CAR is to be returned by the
supplier, usually within a 10-day period. If the form has not been received after 30 days,
purchasing is to send a reminder to the supplier. if the form has not been received after
45 days, quality assurance may withhold acceptance of all further shipments from the
supplier until the requirement is complied with.
5.7 After receipt of the CAR from the supplier, it is
reviewed by quality engineering, which can request additional data from the supplier.
5.8 In-house CAR'S issued will be responded to within
five (5) working days. Adjustments to allotted response time will be issued by the quality
assurance manager only. If the completed CAR has not been received within the allotted
time, another CAR will be issued. If there is no response to either CAR it will be
escalated to the president of the company.
QP #08
POLICIES AND PROCEDURES
QUALITY PROCEDURES
SUBJECT: VENDOR SURVEY
1.0 PURPOSE
This procedure describes the method for surveying candidate
suppliers and subcontractors to gather information relative to their capabilities for
confirming to quality requirements.
2.0 APPLICATION
Vendor surveys are used to gather information from potential
suppliers and subcontractors who are candidates for all levels of procurement activity.
The quality engineering department is responsible for conducting these surveys, for use by
the purchasing department to establish and/or maintain the approved vendors list.
3.0 ASSOCIATED DOCUMENTS
3.1 QUALITY PROCEDURES
- QP-04 RECEIVING INSPECTION
- QP-09 VENDOR RATING
- QP-14 STATISTICAL QUALITY CONTROL
3.2 FORMS
QA #011 VENDOR SURVEY AND TABLES I & II (SHORT FORM)
3.3 APPROVED VENDORS LIST
SPC Vendor rating graphs (computer)
4.0 PROCEDURE - ON SITE WITHIN 100 MILES
4.1 Request for quality surveys of candidate suppliers
or subcontractors can be generated by program management, purchasing, or quality
assurance.
4.2 Authorization to conduct a quality survey of a
candidate supplier or subcontractor can be given by either quality assurance or purchasing
department management personnel.
4.3 Surveys are to be conducted by the quality
engineering department. If a team is to make the survey, the team members are to be
selected from the quality engineering organization (team leader), purchasing, program
management, and engineering.
4.4 The purchasing department is responsible for
making formal survey arrangements with a candidate supplier or subcontractor, including
explaining the purpose of the survey, and scheduling a date and time.
4.5 Survey is not to begin at a supplier's or
subcontractor's facility without an initial introductory discussion with the appropriate
supplier/subcontractor management representative.
4.6 At the conclusion of a survey, the
supplier/subcontractor management representative is to be verbally briefed as to the
findings. Official survey results will later be transmitted by letter/fax.
4.7 The quality engineering department is to evaluate
the survey findings and generate a supplier quality evaluation report. This form is to be
used for all surveys of potential suppliers and subcontractors who may be involved in any
level of procurement activity.
4.8 If a supplier is found to be acceptable, it is
placed on the "Approved Vendors List". Quality engineering's evaluation will
determine the category for which the vendor is approved. (See Table I and II).
4.9 Resurveys may be conducted when the following
conditions exist:
- CRITICAL OR NEW PROCESS ARE ADDED TO THE PROCUREMENT
- SUPPLIER OR SUBCONTRACTOR ACQUIRES A NEW FACILITY OR NEW
MANAGEMENT
- VENDOR SCORE FALLS BELOW 97% ON VENDOR RATING, FOR A PERIOD OF
90 DAYS
5.0 PROCEDURE-OUTSIDE 100 MILES
5.1 QUALITY PROCEDURES SAME AS 3.1 OF THIS PROCEDURE.
5.2 FORMS
Same as 3.2 of this procedure
5.3 APPROVED VENDORS LIST
Same as para: 3.3 of this procedure
5.4 Vendors outside 100 miles, mail or fax form QA
#011.
5.5 Quality engineering will review returned forms for
completeness and compare to QP #09 and QP #14. When found to be compliant to requirements
for commodities and rating levels add to approved list.
TABLE I
SPECIAL PROCESS CODES
CODES
AA PRINTED CIRCUIT BOARDS
BB CASTING
CC BRAZING
DD WELDING
EE METAL FINISHING
FF HEAT TREATING
GG NONDESTRUCTIVE TESTING
HH CONFORMAL COATING
II ELECTRONIC COMPONENTS
JJ ENVIROMENTAL EQUIPMENT
KK ELECTRONIC EQUIPMENT
LL PRIME/PAINT
TABLE II
COMMODITY CODES
CODE COMMODITY
A STANDARD HARDWARE ITEMS (SCREWS, NUTS, BOLTS, ETC.)
B. STANDARD ELECTRONIC COMPONENTS (CAPACITORS, RESISTORS,
IC'S ETC.)
C. STANDARD WIRE OR CABLE
D. STANDARD ELECTRONIC EQUIPMENT (POWER SUPPLIES,
OSCILLOSCOPES, ETC.)
E. STANDARD ITEMS (MISC.)
F. FABRICATED ITEMS - SHEET METAL
G. FABRICATED ITEMS - MACHINING
H. FABRICATED ITEMS - CASTINGS
I. FABRICATED ITEMS - ELECTRONIC COMPONENTS
J. FABRICATED ITEMS - ELECTRONIC ASSEMBLIES
K. FABRICATED ITEMS - ELECTRONIC EQUIPMENT
L. FABRICATED ITEMS - PRINTED CIRCUIT BOARDS
M. FABRICATED ITEMS - WIRE HARNESSES/CABLES
N. FABRICATED ITEMS - MISCELLANEOUS
O. SERVICES - ELECTRONIC COMPONENTS TESTING
P. SERVICES - ENVIRONMENTAL TESTING
Q. SERVICES - ENGINEERING CONSULTANTS
R. SERVICES - PAINTING
S. SERVICES - METAL FINISHING
T. SERVICES - MARKING/SILK-SCREEN/ENGRAVING
U. SERVICES - MISCELLANEOUS
QP #09
POLICIES AND PROCEDURES
QUALITY PROCEDURES
SUBJECT: VENDOR RATING
1.0 PURPOSE
The procedure defines the method for rating the quality
performance of suppliers and subcontractors.
2.0 APPLICATION
This procedure entails the evaluation, rating, and reporting
by the source inspection and receiving inspection departments of the quality performance
of all suppliers and subcontractors.
3.0 ASSOCIATED DOCUMENTS
3.1 QUALITY PROCEDURE
- QP #04 RECEIVING INSPECTION
- QP #14 STATISTICAL QUALITY CONTROL
3.2 FORMS
- SPC Graphs "P" chart
- SPC Graphs "C" chart
- QA# "P" chart data
3.3 REPORT
APPROVED VENDORS LIST
4.0 PROCEDURE
4.1 The evaluation and rating of
supplier/subcontractor performance in terms of quality are the responsibility of the
procurement quality engineering department.
4.2 Evaluations and ratings are to be made on a
monthly basis.
4.3 Source material to be used in evaluating and
rating supplier/subcontractor performance include, but are not limited to, source
inspection reports and receiving inspection records.
4.4 The vendor rating is a simple calculation of
percent defective: The total number of accepted parts divided by the total number of parts
inspected. This calculation is made over the last five (5) consecutive lots (max.). If
five lots are not completed, quality engineering will calculate from the information
available.
EXAMPLE: LOT NO. PARTS ACCEPTED PARTS INSPECTED
- 10 10
- 14 15
- 10 10
- 10 10
- 14 15
TOTAL: 55 60
55 DIVIDED BY 60 = .966 = 97% VENDOR RATING
4.5 The vendor ratings will be calculated by quality
engineering and issued monthly in the approved vendors list.
4.6 Copies of the approved vendors list will be
distributed to the quality assurance manager and the purchasing manager also receiving
inspection.
4.7 The purchasing manager is responsible for limiting
or suspending the use of suppliers or subcontractors who consistently rate below 97% on
the rating scales.
4.8 Vendors that fall below 95% will be placed on a
suspect list to be evaluated by quality engineering. If their performance does not
improve, quality engineering will issue a corrective action request per QP-07. Not
improving quality levels within a reasonable time span (30 days).
QP #10
POLICIES AND PROCEDURES
QUALITY PROCEDURES
SUBJECT: CALIBRATION PROCEDURES
1.0 PROCEDURE
This procedure specifies the responsibilities for controlling
the accuracy of measuring an test equipment and measurement standards to assure that
products delivered to customers conform to specified requirements.
2.0 APPLICATION
This procedure applies to the quality control department and
to all departments and individuals who use measuring test equipment. The quality control
department has the prime responsibility for operation of the calibration system.
3.0 DEFINITION
3.1 CALIBRATION: comparing measuring and test
equipment with measuring standards known accuracy, to detect and adjust deviations from
the standards.
3.2 CALIBRATION CONTROL: a documented system for
assuring that measuring and test equipment devices and measurement standards are
calibrated, and that this is done at intervals that assure accuracy.
3.3 CALIBRATION RECALL: a system for indication in
advance for each measuring and test equipment devices and measurement standard the date
when it is next due to be calibrated.
3.4 CALIBRATION INTERVAL: the period of time between
calibration intervals can vary for devices depending upon their stability, purpose, and
degree of usage.
3.5 CERTIFICATION: approval given for the use of newly
acquired or reworked, modified measuring and test equipment devices or processes following
an examination that has verified that they are compatible with other devices to be
processed into the system, and, capable of fulfilling intended functions.
3.6 MEASURING AND TEST EQUIPMENT: all devices used to
measure, gauge, test, inspect, or otherwise examine items to determine compliance with
specifications.
3.7 MEASUREMENT STANDARD (REFERENCE): an instrument or
device of the highest order of accuracy which is used in a calibration system as primary
standard of reference, its accuracy traceable to the nation bureau of standard.
3.8 MEASUREMENT STANDARD (TRANSFER): and instrument or
device in a calibration system used to transfer measurements from the reference standard
to a lower echelon "working" standard or directly to the measuring or test
equipment being calibrated to avoid wear or deterioration of the reference standard.
3.9 MEASUREMENT STANDARD (INTERIM): and instrument
used as standard until an authorized standard is established.
4.0 ASSOCIATED DOCUMENTS
4.1 PROCEDURES
CMP #0005-0010
4.2 FORMS
QA #013, QA #014, QA #015
5.0 PROCEDURE (GENERAL)
5.1 All measuring and test equipment instruments and
devices used to determine item's conformance to specifications requirements are to be
calibrated. This calibration is to occur at regularly schedule intervals (See Table I)
determined on the basis of stability, purpose, and usage or sooner if there is some reason
to believe that the instrument or device needs recalibration.
5.2 All measuring and test equipment devices will be
calibrated to working measurement standards or transfer measurement standards which are
calibrated and certified by the National Institute of Standards and Technology.
5.3 Records are to be maintained that identify each
item of measuring and test equipment, each measurement standard, and list and date of each
instance of calibration, citing measurements and adjustments. The records are to be able
to demonstrate traceability of the calibration work to the National Institute of Standard
and Technology.
5.4 Each item of measuring and test equipment and
measurement standards is to be marked showing the date of the most recent calibration, the
stamp of the technician who performed the calibration, and the date when the next
calibration is scheduled. If the item is to small for this type of marking, a color code
or smaller identifying mark is to be used which is keyed to independently maintained
records that cite the same date.
5.5 Departments using measuring and test equipment are
responsible for monitoring calibration due dates and submitting instruments and devices
for calibration on schedule.
5.6 Inspectors and test technicians cannot accept
measurements values obtained on measuring and test equipment that have exceeded
calibration due dates.
5.7 Measuring and test equipment instruments and
devices cannot be calibrated with measurement standards that have exceeded calibration due
dates.
5.8 Employee-owned measuring equipment (such as
micrometers) can be used for product acceptance measurements only if they are calibrated
by the company on a regularly scheduled basis.
5.9 The environment where measuring and test equipment
instruments and devices are to be both calibrated and used must be controlled to the
extent necessary to assure required accuracy, with consideration given to temperature,
humidity, vibration, cleanliness, and other controllable factors.
5.10 Purchasing is responsible for coordinating with
quality assurance in the selection and acquisition of subcontractors to perform measuring
and test equipment calibration and/or repair work.
5.11 All new, reworked, repaired, or modified
measuring and test equipment instruments and devices are to be examined, ad when proved
acceptable, certified as complying to requirements by the quality control department.
5.12 The quality/control department is responsible for
securing calibration instructions for all measuring and test equipment that has been
procured.
5.13 The quality control department will maintain a
listing of company measuring and test equipment and test equipment that has been
certified.
5.14 The quality control department will be
responsible for procuring and maintaining all measurements standards required to support
product measurement requirements.
5.15 The calibration department will be responsible
for developing measurement standards in those instances where measuring and test equipment
are calibrated in-house.
6.0 PROCEDURE (CONTROL AND RECALL)
6.1 The quality control department is responsible for
the identification, calibration, repair, and calibration record keeping of all measuring
and test equipment devices and all measurement standards. The records must offer
traceability to the national institute of standards and technology.
6.2 All personnel and departments using measuring test
equipment have the responsibility for seeing that an item of equipment is not used when is
calibration period has expired. Such items are to be returned to the quality control
department for calibration arrangements.
6.3 A calibration/service data record is to be created
and maintained for each item of measurement standards, measuring equipment, and test
equipment. It is to be filled out as follows:
- THE ITEM'S NAME AND SERIAL NUMBER
- THE ITEM'S MANUFACTURER
- THE MODEL NAME AND/OR NUMBER
- THE RECALL DATE OR DATES
- THE CALIBRATION/SERVICE SPECIFICATION NUMBER
- THE CALIBRATION/SERVICE RECORD (CSDR) NUMBER (TO BE ASSIGNED
BY THE PERSON FILLING OUT THIS FORM)
- THE CALIBRATION JOB INSTRUCTION NUMBER
- THE DATE THIS RECORD IS FIRST CREATED
- THE SIGNATURE OF THE PERSON APPROVING THE BASIC RECORD
- A LISTING OF THE MEASUREMENT STANDARD OR STANDARDS REQUIRING
TO CALIBRATE THIS ITEM.
6.4 Actual measurement date is recorded in terms of:
- THE OPERATION NUMBER
- THE PARAMETER
- NOMINAL
- MEASURED READING OR VALUE
- CORRECTED READING OR VALUE
- MINIMUM LIMITS
- MAXIMUM LIMITS
- REMARKS
6.5 Calibration and repair status identification is
accomplished through the use of decals applied to each item of measurement standards,
measuring equipment, and test equipment. These decals are as follows: a calibration due
decal, which shows the date when the next calibration stamp of the person who performed
the work; a not calibrated decal, which carried the notice that the item of equipment to
which this decal is attached is not to be used for official measurement proposes; and
out-of-service decal, and with the notice that the equipment to which the decal is
attached, must be repaired and/or calibrated before use. It carries the name or stamp of
the person who has determined that this condition exists and the date.
6.6 The quality control department has the
responsibility for continually examining the calibration intervals assigned to the
measurement devices and extending or shortening them as required.
6.7 Calibration of a measurement device can be
requested at any time, regardless of the calibration due date for that device, following
the occurrence of any event that places the devices accuracy in doubt.
6.7.1 Equipment that has an out of tolerance
condition, fails calibration, or whose tamper proof seal is broken, requires quality
engineering to assess the appropriate corrective action (QP-07) as follows:
- Remove failed equipment from process.
- Identify material, parts, or assemblies tested within
calibration cycle of failed equipment.
- Formal notification to customer any interdepartmental
functions of material, parts or assemblies that may require investigative actions.
- Repair/replacement of failed equipment prior to use in any
process upon discovery.
- Issue formal corrective action per QP #07 of this manual.
6.8 The quality engineering department is to maintain
a surveillance function, its purpose to periodically and randomly audit compliance to the
calibration control and recall system. Violations are to be reported to the manager of
quality assurance.
6.9 Tamper proof seals/labels. Items having dials,
levers and or knobs that must remain positioned for purposes of calibration, i.e.: ovens,
electronic test equipment, etc., etc., must have a tamper proof seal located so as to
prevent any change in calibration parameters.
TABLE I
CALIBRATION INTERVALS
ITEM NUMBER FORMAT INTERVAL MONTHS
MECHANICAL
- Micrometers MCXXX 6
- Vernier Calipers VCXXX 6
- Height Gages HGXXX 6
- Snap Gages SGXXX 6
- Thread Gages TGXXX 6
- Dial Calipers DCXXX 6
- Dial Indicators DIXXX 6
- Flow Meters FMXXX 6
- Barometers BMXXX 6
- Thermometers TMXXX 6
- Hydrometers HMXXX 6
- Pressure Gages PGXXX 6
- Torque Wrenches TWXXX 6
- Crimping Tools CTXXX 6
- Measuring Stands MSXXX 12
- Plug Gages PGXXX 12
- Sine Bars SBXXX 12
- Angle Blocks ABXXX 12
- "V" Blocks VBXXX 12
- Radius Gages RGXXX 12
- Hardness Tester HTXXX 12
- Parallels PLXXX 12
- Surface Plate SPXXX 36
- Gage Blocks GBXXX 36
- Angle Gage Blocks ABXXX 36
ELECTRICAL
- V-O-M meters VMXXX 6
- Network Analyzers NAXXX 12
- Frequency Counters FCXXX 12
QP #11
POLICIES AND PROCEDURES
QUALITY PROCEDURES
SUBJECT: INSPECTOR/OPERATOR TRAINING AND CERTIFICATIONS
1.0 PURPOSE
This procedure establishes the requirements for training,
certifying, and recertifying employees involved in performing critical and specialized
functions.
2.0 APPLICATION
This procedure applies to employees performing critical
and/or specialized functions related to deliverable items. Based on customer imposed
specification per contact.
2.1 RECERTIFICATION SHALL BE REQUIRED UNDER THE
FOLLOWING CIRCUMSTANCES:
A. PROFICIENCY REQUIREMENTS HEREIN ARE NOT MET.
B. NEW TECHNIQUE HAVE BEEN DEVELOPED WHICH REQUIRE NEW SKILLS.
C. WORK PERIOD INTERRUPTION EXCEED 90 DAYS.
D. THERE IS REASON TO QUESTION PROFICIENCY OR WORKMANSHIP.
3.0 ASSOCIATED DOCUMENTS
3.1 PROCEDURES
CMP #0011-0020
3.2 FORMS
QA #016
4.0 PROCEDURE
4.1 The responsibility for developing training courses
and testing criteria, operation of the training session, and conducting certification
sessions falls under the jurisdiction of the quality and production departments.
4.2 The quality engineering department is responsible
for examining customer-imposed specifications related to inspector/operator certification,
and accommodating these requirements.
4.3 Notification of employees of certifications or
recertifications sessions will be accomplished throughout the use of an internal
memorandum.
4.4 An inspector/operator unable to attend the session
as scheduled, is to have their supervisor arrange a new date by contacting the person who
prepared the notice.
4.5 The sessions are to be conducted by company
engineering personnel and are to cover familiarity with the applicable specifications,
procedures and instruction, the performance of tasks related to the job classification,
and the techniques for maintaining records and preparing reports.
4.6 The quality assurance department is responsible
for maintaining records of the certification/recertification program. The quality
certification record form is to be used for this purpose. It is to be filled out as
follows:
- THE EMPLOYEE'S NAME (LAST NAME FIRST).
- THE EMPLOYEE'S IDENTIFICATION NUMBER.
- THE DEPARTMENT TO WHICH THE EMPLOYEE IS ASSIGNED.
- THE EMPLOYEE'S JOB CLASSIFICATION.
- THE CERTIFIABLE FUNCTION BEING COVERED BY THIS EMPLOYEE'S
TRAINING AND CERTIFICATION SESSIONS.
- THE DATES AND RELATED COMMENTS CONCERNING THE CERTIFICATION
EXPIRATION DATES FOR THIS EMPLOYEE.
- THE DATES AND COMMENTS RELATED TO AUDITS MADE OF THIS
EMPLOYEE'S PERFORMANCE.
4.7 Periodically, and at random, the quality assurance
personnel are to audit the performance of certified personnel and report the findings on
the previously described quality certification record. As a result of this audit, and
employee can be required to be retrained and recertified, (regardless of the expiration
date on their current certification) if the amount of errors and/or problems with quality
warrant such action.
QP #12
POLICIES AND PROCEDURES
QUALITY PROCEDURES
SUBJECT: IN-PROCESS INSPECTION
1.0 PURPOSE
This procedure established the method for monitoring and
controlling the quality of parts, components, and subassemblies throughout the various
intermediate steps involved in the manufacturing process.
2.0 APPLICATION
This procedure applies to the in-process quality control
department of quality assurance, and excludes source and receiving inspection, and final
inspection and test.
3.0 ASSOCIATED DOCUMENTS
3.1 QUALITY PROCEDURES
- QP-05 FIRST ARTICLE INSPECTION
- QP-07 CORRECTIVE ACTION
- QP-03 NON-CONFORMING MATERIAL CONTROL
- QP-17 ISSUING QUALITY INSTRUCTIONS
- QP-18 CONTROL OF INSPECTION STAMPS
3.2 FORMS
QA #005, QA #006, QA #008, QA #009, QA #110, QA #112
4.0 PROCEDURE
4.1 Parts, components, and subassemblies, through
their intermediate stages of manufacturing, are to be periodically presented for
inspection by manufacturing. These inspections are to take place, as called for, on the
production router and on the project inspection plan. When there is an occurrence of some
nature that indicates that special inspections are appropriate, a quality engineer will
issue quality instructions per procedure no. QP-17.
4.2 Inspection methods employed can include
inspections by machine operators and witnessed by inspection personnel, the use of
automated inspection gauges, moving line, lot sampling, set-up/fixture approval or first
piece approval, production line inspection station, roving inspectors.
4.3 Inspections are to be made using applicable
inspection instructions, drawings, specifications, and other appropriate reference
materials and/o charts (XER,U,C,P Charts).
4.4 The in-process inspector is to secure the required
gauges or test instruments required.
4.5 The inspection is to include an examination of the
accompanying paper work for completeness and correctness, workmanship, physical and
functional characteristics, and when called for the effectiveness of special process such
as heat treating or the application of special coating.
4.6 The inspector must verify any special testing or
laboratory analysis performed as designated on the production router.
4.7 First piece inspections are to be recorded on the
P Chart Data Log. This is to be filled out as follows:
- THE DATE OF THE INSPECTION
- THE NAME OF THE PART BEING INSPECTED
- THE REVISION NUMBER
- THE PART NAME
- THE SUBMITING DEPARTMENT
- THE RESULTS OF INSPECTION (REJECTS, DEFECTS, ETC.)
- THE INSPECTOR'S STAMP
- THE MRR NUMBER (IF APPLICABLE)
4.8 Parts or assemblies, when specified, found to be
acceptable are to be so marked using an inspection stamp and tagged with a green tag. The
production router must also be stamped so material can continue in their normal flow
through the manufacturing process.
4.9 A material reject report is to be filled out when
parts or assemblies are found to be discrepant. A red tag will be placed on the material
identifying mrr no., part no., serial no., date, quantity, inspection reject stamp. The
form should be filled out as follows:
- THE REPORT NUMBER
- THE PART OR ASSEMBLY NUMBER
- THE PART OF ASSEMBLY NAME
- THE DATE OF THE REPORT
- PROGRAM/PROJECT NUMBER
- THE LOT NUMBER OR SERIAL NUMBER OR NUMBER RANGE
- THE QUANTITY SAMPLED
- THE QUANTITY REJECTED
- THE DEPARTMENT
- THE NAME OR STAMP MARK OF THE INSPECTOR
- THE QUANTITY
- THE REASON FOR REJECTION
- REWORK INSTRUCTIONS GENERATED BY MANUFACTURING REPRESENTATIVE
Following a preliminary examination involving product
engineering and quality engineering, a disposition will be made per from QP-03. If the
disposition requires corrective action, a corrective action request (Form No. QP-009) will
be issued per Form No. QP-07.
4.10 On a regular basis, the in-process quality
control department is to review all inspection instructions, determine their correctness
and effectiveness, and coordinate changes, if required, with the quality engineering
department.
5.0 IN PROCESS TEST MONITORING
5.1 When any necessary functional testing is
performed, as required, by production personnel the quality control function performs
surveillance inspections of the functional tests, assuring verification of units to
customer contractual requirements.
5.2 Non-conforming assemblies are processed in
accordance with QP-04 of this manual.
5.3 Corrective action is taken in accordance with
QP-07 of this manual.
5.4 Test instructions are issued in written form, as
applicable, with consideration given to the complexity of the item and the customer
requirements. The instruction include criteria for acceptance and rejection. This shall be
developed by the test engineering department and approved by the customer when deemed
appropriate.
QP #13
POLICIES AND PROCEDURES
QUALITY PROCEDURE
SUBJECT: FINAL INSPECTION
1.0 PURPOSE
This procedure established the methods and responsibility for
final inspection, testing and packaging of completed products to assure that they comply
with company standards and customer requirements.
2.0 APPLICATION
This procedure applies to the inspection of all deliverable
finished goods.
3.0ASSOCIATED DOCUMENTS
3.1 QUALITY PROCEDURES
- QP-05 FIRST ARTICLE INSPECTION
- QP-03 NON-CONFORMING MATERIAL CONTROL
- QP-07 CORRECTIVE ACTION
- QP-17 ISSUING QUALITY INSTRUCTIONS
- QP-18 CONTROL OF INSPECTION STAMPS
3.2 FORMS
QA #005, QA #006, QA #008, QA #009, QA #110, QA #112
4.0 PROCEDURE
4.1 All finished goods are to be presented to final
inspection for inspection. These inspection are to take place as called for on the
production router and/or the project inspection plan. When there is an occurrence of some
nature that indicates special inspections, quality engineering will issue quality
instruction per procedure no. QP-17.
4.2 Parts and assemblies will not be accepted for
final inspection unless all operations are called out on the production router and are
identified as completed.
4.3 Inspections are to be made using applicable
inspection instructions, drawings, specifications, and other appropriate reference
materials.
4.4 The inspection is to include an examination of
accompanying paper work for completeness and correctness, workmanship, physical and
functional characteristics, and the proper markings on parts and assemblies.
4.5 The inspector must verify any testing or
laboratory analysis performed as designated on the production router.
4.6 Products are to be approved for acceptance testing
by final inspection and tested after a determination has been made that the product is
complete, that all operations have been completed, and that there are no open items.
4.7 Each acceptance test is to be witnessed by CMC QA
and/or the customer's representative.
4.8 Quality engineering is responsible for monitoring
the test area to make sure test equipment that has passed its calibration due date is not
used.
4.9 Final inspection is responsible for overseeing the
proper packaging of finished goods prior to shipment. This includes making sure packaging
specifications are being complied with, and making certain that all interior and exterior
containers are properly marked.
4.10 Final inspection is responsible for overseeing
the proper shipment of goods, including verifying that the shipping, test and customer
required documents are correct and properly stamped, and that interstate commerce
commission regulations and other applicable requirements are complied with.
4.11 Parts or assemblies, found to be acceptable are
to be so marked using and inspection stamp and tagged with a green tag. The production
router must also be stamped so material can continue in their normal flow.
4.12 A material reject report is to be filled out when
parts or assemblies are found to be discrepant. A red tag will be placed on the material
identifying MRR no., part no., serial no., date, quantity, inspection reject stamp. The
form should be filled out as follows:
- THE REPORT NUMBER
- THE PART OR ASSEMBLY NUMBER
- THE PART OR ASSEMBLY NAME
- THE DATE OF THE REPORT
- PROGRAM/PROJECT NUMBER
- THE LOT NUMBER OR SERIAL NUMBER OR NUMBER RANGE
- THE QUANTITY SAMPLED
- THE QUANTITY REJECTED
- THE DEPARTMENT
- THE NAME OR STAMP MARK OF THE INSPECTOR
- THE QUANTITY
- THE REASON FOR REJECTION
- THE REWORK INSTRUCTIONS GENERATED MANUFACTURING REPRESENTATIVE
Following a preliminary examination involving product
engineering and quality engineering, a disposition required corrective action, a
corrective action request will be issued per form no. QA# 009.
4.13 On a regular basis, the quality control
department is to review all inspection instructions, determine their correctness and
effectiveness, and coordinate changes, if required, with the quality engineering
department.
QP #14
POLICIES AND PROCEDURES
QUALITY PROCEDURES
SUBJECT: STATISTICAL QUALITY CONTROL
1.0 PURPOSE
This procedure sets forth the methodology for establishing
data gathering techniques for the systematic and scientific measurement of quality control
and manufacturing processes through the use of statistics and statistical analysis.
2.0 APPLICATION
Statistical quality control is focused at obtaining control
of manufacturing processes at CMC and CMC's suppliers/vendors.
3.0 GOALS
The overall goal of statistical quality control and
statistical process control is to increase the proficiency of performance and thereby
reduce the costs.
4.0 ASSOCIATED DOCUMENTS AND HANDBOOKS:
- QP-04 NON-CONFORMING MATERIAL
- QP-05 RECEIVING INSPECTION
- QP-06 FIRST ARTICLE INSPECTION
- QP-07 SOURCE INSPECTION
- QP-10 VENDOR RATING
- QP-13 IN-PROCESS INSPECTORS
- QP-14 FINAL INSPECTION
- QP-16 QUALITY AUDITS
- WESTERN ELECTRIC STATISTICAL QUALITY CONTROL HANDBOOK
- AMERICAN SOCIETY FOR QUALITY CONTROL GLOSSARY AND TABLES FOR
STATISTICAL QUALITY CONTROL
- IBM QUALITY INSTITUTE HANDBOOK
5.0 CHARTS AND CHART DEFINITIONS
"P" CHART: UNITS INSPECTED - UNITS REJECTED.
(GO/NO GO): N/P
"C" CHART: DEFECTS FOUND PER REJECTED
"U" CHART AVERAGE DEFECTS PER REJECTED
"X BAR AND R CHART: AVERAGE OF ALL READINGS AND
DIFFERENCE between HIGHEST AND LOWEST READING.
PARETO PRINCIPLE: IDENTIFIES SIGNIFICANT FEW FROM
INSIGNIFICANT MANY, IN A STAIR-STEP MANNER AND A PARETO CHART.
CMC WORKING CHARTS: CHARTS USED INTERNALLY THAT REFLECT
COMPANY WIDE PROGRAMS; REJECT %, DEFECTS ON PROGRAMS AND OPERATOR RESPONSIBILITY.
6.0 PROCEDURE
I. Date to be inputted daily
A. "P" CHART DATA
B. SUPPLIER/VENDOR
II. Review and analyze weekly charts
A. "P" CHART
"C" CHART
PARETO CHART
B. Any and all charts that reflect date point 1.5% reject rate
at or above upper warning level (2 sigma)
C. Any and all charts that reflect out of control limits,
which falls below 97% acceptance or above 3% reject percentage.
D. Pareto chart must be developed on each and every program
that is out of control at or above 3.1% reject rate.
III. Charts Published Weekly (Department Supervisor)
- A. Published on every Monday
- All charts known as CMC working charts
- All charts and graphs are to be reviewed by the SPC
Coordinator/team
- Published to all departmental supervisors
IV. CHART PUBLISHED MONTHLY
A. P CHARTB. C
CHART
C. PARETO
D. OPERATOR RESPONSIBILITY
E. All charts by program accept and reject composition
QP #15
POLICIES AND PROCEDURES
QUALITY PROCEDURES
SUBJECT: QUALITY AUDITS
1.0 PURPOSE
This procedure sets forth the method for periodically and
randomly examining products and systems to determine the effectiveness of the overall
quality assurance program.
2.0 APPLICATION
This procedure applies to all internal functions
3.0 DEFINITIONS
Quality audit: An official examination of products and
systems, taking place on a periodic by random, unannounced basis, to verify the
effectiveness of the company's quality program.
4.0 FORMS
QA #017, QA #28
5.0 PROCEDURE
5.1 The quality assurance department has the
responsibility for planning and conduction quality audits.
5.2 Quality assurance will prepare a audit plan using
QA Forms #017. All portions of each form must be filled out completely. Quality assurance
will use inter-department procedures and quality procedures to format the audit.
5.3 The audit plan must be reviewed and approved by
the quality assurance manager prior to doing the audit.
5.4 Auditor will notify each department manager as to
when they will be in their area prior to doing the audit. NOTE: It is the manager
descretion to assign someone to walk throughout the audit with the auditor.
5.5 Auditor will be thorough and extensive when
performing audits. The detailed description of the audit plan will be researched by each
individual item to assure the effectiveness of the audit. Auditor will have access to all
material and documentation deemed necessary to perform an accurate and effective audit.
5.6 At the conclusion of the audit the auditor will
review all discrepancies, if any, with each department manager.
5.7 If corrective actions are issued follow QA-07.
QA #16
POLICIES AND PROCEDURES
QUALITY PROCEDURES
SUBJECT: GOVERNMENT/CUSTOMER PROPERTY CONTROL
1.0 PURPOSE
This procedure describes the method for providing adequate
inspection, storage, and maintenance of property furnished by the government or customer.
2.0 APPLICATION
This procedure applies to all furnished material unless
excluded from these requirements by contractual agreement.
3.0 ASSOCIATED DOCUMENTS
4.0 PROCEDURE (GOVERNMENT)
4.1 Upon receipt, receiving inspection is to examine
all customer-furnished materials for the following:
- TRANSIT DAMAGE
- COMPLETENESS AND PROPER TYPE
- PROPER IDENTIFICATION
The quantity is also to be verified.
4.2 If appropriate and per contractual agreement, the
materials are to be functionally tested to determine satisfactory operation and a GFP#
issued and GFP sticker applied.
4.3 If material is defective, procedure QP-04
(non-conforming material control) is in effect.
4.4 Quality engineering is responsible for conducting
periodic audits to assure that the materials are being properly stored, adequately
protected, subjected to periodic maintenance when required, and that precautions exist to
protect them from improper use or disposition.
4.5 Quality engineering is responsible for reporting
damage, malfunction, or otherwise unsuitable furnished materials. If the problem is
detected after installation, then the report is to contain an indication of the probable
cause.
4.6 Quality assurance management is responsible for
maintaining complete and accurate records of all furnished materials and making these
records available for reviewing by the "government property log book".
5.0 PROCEDURE (CUSTOMER)
5.1 Customer furnished equipment shall be examined
upon receipt to detect and identify any existing deterioration, damage, etc.
5.2 Items shall be inspected to ascertain correctness
and completeness.
5.3 Any deficiencies shall be documented and the
contracting officer and/or appropriate customer personnel shall be notified in writing.
5.4 A control log shall be maintained by the Quality
Assurance function of all customer furnished equipment. The log will include item
received, date received, description, serial number, contract number and any other
applicable data.
5.5 Periodic inventory and inspection shall be made to
verify the status of the equipment and assure adequate storage, handling, etc.
5.6 Shipping documents shall indicate the appropriate
serial number off the equipment. The control log shall be updated to reflect the shipment
and date of the items.
5.7 Customer furnished measuring and test equipment
shall be controlled in accordance with QP-11 of this manual (calibration).
5.8 Each item of customer furnished equipment shall be
tagged or labeled. The identification marker shall contain indication of CFE and
sufficient additional information to allow reference to the control log.
5.9 When customer furnished equipment is
shipped/returned the date of shipment shall be entered in the control log to terminate
control of the item.
6.0 PROCEDURE (CPFF CONTRACTS, RESIDUAL MATERIALS)
6.1 The quality assurance function shall have the
responsibility of surveillance of any residual materials and supplies.
6.2 The quality assurance function will assure that
any residual parts presented for stock and/or storage are properly identified as to
inspection status, part number, drawing number including revision, and quantity. The parts
shall be packaged adequately to prevent deterioration or damage.
6.3 Residual parts which are contractually property of
the customer will be properly segregated until customer direction regarding their
disposition has been received.
QP #17
POLICIES AND PROCEDURES
QUALITY PROCEDURES
SUBJECT: ISSUANCE OF QUALITY INSTRUCTIONS
1.0 PURPOSE
This procedure provides a system for preparing, issuing, and
maintaining instructions for the inspection of specific parts, assemblies, subassemblies
and processes.
2.0 APPLICATION
This procedure applies to personnel in the quality assurance
department who are responsible for the preparation product quality factors that are not
covered in present procedures.
3.0 ASSOCIATED DOCUMENTS
CMP #0047 PARA: E
3.1 FORMS
QA #021
4.0 PROCEDURE
4.1 Quality engineering obtains and reviews the
production department's procedures for the part, assembly, subassembly, or processes for
which quality instructions are to be prepared.
4.2 Quality engineering develops and issues the
project inspection plan for the part, assembly, subassembly, or processes for which
quality instructions are to be prepared.
4.3 Quality engineering develops and issues the
sampling method for the part, assembly, subassembly, or processes for which quality
instructions are being prepared.
4.4 The quality instructions should include the
following information:
FORM QA #021
- THE INSTRUCTION NUMBER
- THE PAGE NUMBER
- THE NAME OF THE PROGRAM OR PROJECT
- THE CONTRACT NUMBER
- THE NAME OF THE PART OR ASSEMBLY
- THE NUMBER OF THE PART OF ASSEMBLY
- THE NAME OF THE PERSON PREPARING THE INSTRUCTION
- THE INSTRUCTION-PREPARATION COMPLETION DATE
- THE INSPECTION OR TEST POINT NUMBER (DERIVED FROM QUALITY
PLAN)
- THE DETAILED INSTRUCTION INCLUDING A LISTING OF THE DOCUMENTS
THAT ARE ESSENTIAL TO THE PROCESS INCLUDING DRAWINGS, SPECIFICATIONS, AND TEST PROCEDURES
AS WELL AS AN IDENTIFICATION OF THE EQUIPMENT REQUIRED AT EACH TEST OR INSPECTION POINT.
- SAMPLE PLAN PER STATISTICAL TREND DATA (AQL).
4.5 In preparing quality instructions, specify, when
needed, proper handling, preservation, storage, packaging, and shipping instructions to
protect the product's quality and to prevent damage, deterioration, and degradation.
4.6 The completed instruction is to be reviewed by
quality assurance management, signed and dated, then issued for application.
4.7 The quality assurance department has the
responsibility for maintaining a comprehensive cross-reference file of all quality
instructions.
4.8 This procedure includes Coleman Microwave and
supplier/vendor's processes and programs.
QP #18
POLICIES AND PROCEDURES
QUALITY PROCEDURES
SUBJECT: CONTROL OF INSPECTION STAMPS
1.0 PURPOSE
This procedure sets forth the requirements for issuing, using
and controlling the quality inspection and identification stamps that are required for
quality assurance personnel.
2.0 APPLICATION
This procedure applies to personnel associated with the
issuance, use, and/or control of quality inspection.
3.0 FORMS
3.1 QA #018 RECEIPT-QUALITY INSPECTION AND
IDENTIFICATION STAMPS
- QA #019 CONTROL LOG-QUALITY INSPECTION AND IDENTIFICATION
STAMPS
4.0 PROCEDURE
4.1 Quality inspection and identification stamps will
be made of rubber (for use with permanent ink).
4.2 Each stamp will be identified with a unique
number, uniquely assigned to a specific individual.
4.3 The types of stamps are illustrated in figure 1,
quality inspection and identification stamp. Their uses are as follows:
1A Source inspection acceptance stamp indicates materials that
have been inspected and accepted at a supplier's facility1B In-process inspection acceptance stamp is used to identify partially
processed materials including subassemblies that have been inspected to their current
stage of completeness and found to be acceptable.
1C Final inspection acceptance stamp is used to identify
completed materials that have been inspected prior to shipment or storage and found to be
acceptable.
2. Quality control receiving inspection is used to identify
the acceptance of piece parts, fabricated metals, PCBA coming in from vendors.
3. Test acceptance stamp indicates parts and assemblies
tested and found to be functionally acceptable.
4. Discrepancy material stamp is used to identify materials
that have failed to pass inspection or test.
5. Equipment calibration stamp is used to identify testing
equipment and measuring devices that have been calibrated to acceptable standards.
6. Quality engineering stamp indicated approval by quality
engineering.
4.4 Responsibility for issuing and controlling quality
inspection and identification stamps is vested by quality assurance management.
4.5 One or more stamps, all with the same identifying
number, will be issued to a qualified person using Form No. QA #018 receipt-quality
inspection and identification stamps. The receipt contains the following:
- DATE THE RECEIPT IS RECORDED
- THE RECORDER'S IDENTIFICATION NUMBER
- THE RECORDER'S NAME, JOB TITLE, DEPARTMENT
- AN IMPRESSION OF THE STAMP
- A DESCRIPTION OF THE STAMP
- RECIPIENT'S SIGNATURE, ACKNOWLEDGING RECEIPT OF STAMP AND
UNDERSTANDING OF COMPANY PROCEDURE RELATED TO USE OF THE STAMP
- ISSUER'S SIGNATURE
4.6 A separate record of stamps, by stamp number, is
to be maintained using form no. QA #019 the control log-quality inspection and
identification stamps form displayed in figure 3 for each stamp, the following information
is recorded:
4.7 The stamp receipt is the only person permitted to
use the assigned stamp and is responsible for keeping it clean and its impressions
legible. Worn stamps must be replaced.
4.8 The stamp recipient is responsible for immediately
reporting, in writing, the loss of a stamp to quality management.
4.9 Quality assurance management is responsible for
the immediate preparation and distribution of a quality bulletin announcing the loss of a
stamp and citing the date when its use will not be valid.
4.10 Stamps returned because of transfer or
termination shall not be reissued for 6 months. The numbers of stamps that have been lost
shall not be reused for 24 months after their reported lost.
- STAMP CONFIGURATION
- SOURCE, IN-PROCESS, FINAL INSPECTION STAMP
- QUALITY CONTROL, RECEIVING INSPECTION
- TEST ACCEPTANCE STAMP
- DISCREPANT MATERIAL STAMP
- EQUIPMENT CALIBRATION STAMP
- QUALITY ENGINEERING STAMP
|